
To ensure that the tool could enter the through-hole and perform the same on the backside of the part, implementation of lighter-diameter filaments and lighter gauge stem wire was the plan. The major diameter of the Flex-Hone used is large enough to treat the breakout burr on the surface of the part. Miller states the solution was to provide a tool much larger in diameter than would normally be used in the through-hole diameter. To perform all the deburring and edge radiusing required, simultaneously, a special Flex-Hone was needed." "To complicate matters further, the tool could only enter the front side of the part. This application became additionally complicated when BRM needed to provide a tool that could also pass through the hole and perform the same deburring and radiusing on the backside of the hole. The application soon expanded to removal of the micro-burr left on the surface at the major diameter of the countersink. The carbide radial COFA deburring tool will remove the burr, followed by the Flex-Hone, which rounds the transitions of the edge breaks.Miller relates their experience when contacted by the surface-finishing laboratory of a major jet engine manufacturer: "The problem at hand was to provide an edge radius at the transition of the chamfer and through-hole. Large burr formations in stainless, Inconel 718, or titanium alloys are very difficult to deburr.

"They do this, not only because it is an efficient way to achieve the very stringent tolerances required, but also because there simply is not another method of doing the work that is sufficiently stable and repeatable." Gary Brown, vice president and general manager, Heule Tool of North America, explains that currently, "A major jet engine component manufacturer uses the Huele-BRM tool combination for finishing chamfered holes on rotating engine parts. This is a patented design that incorporates a unique TiN- or TiAlN-coated carbide blade that allows for faster feeds and speed, providing exceptionally long tool life. Next in this process is the COFA tool blade, available in sizes from 0.157" to 1.614", it cuts a smooth tapered edge break from 0.005" to 0.020", based on the tool size.
Laminate edge blending trial#
Using this tool, exact chamfer diameters can be set without trial and error. As a double-bladed chamfering tool, it creates pre-adjusted front and back chamfers in a single pass without stopping or reversing the spindle. The DEFA precision chamfering tool is available in sizes from 0.157" to 1.750". Based in Cincinnati, OH, Heule Tool of North America, a subsidiary of Heule Werkzeug AG, offers this solution. In combination with the Flex-Hone tool, for the flawless finishes required, most shops should standardize use with a Heule DEFA precision chamfering tool and COFA universal deburring tool, prior to implementation of the miniature Flex-Hone tool. As a flexible, relatively low-cost tool, it is utilized in the manufacturing marketplace for ultra-fine surface finishing, deburring, plateau finishing, and edge blending. Available in standard sizes as small as 4mm in diameter, with custom sizes and abrasives available, the small abrasive globules permanently mounted to flexible filaments characterize the tool. This is where the Flex-Hone tool comes in. In so doing, they recommend, or require, that their suppliers incorporate them as well. Many major manufacturers in jet aviation are adopting advanced, hands-off hole drilling, edge breaking, and deburring techniques. Navy published a Quality Hole specification several years ago, and that it includes the Flex-Hone for this purpose.
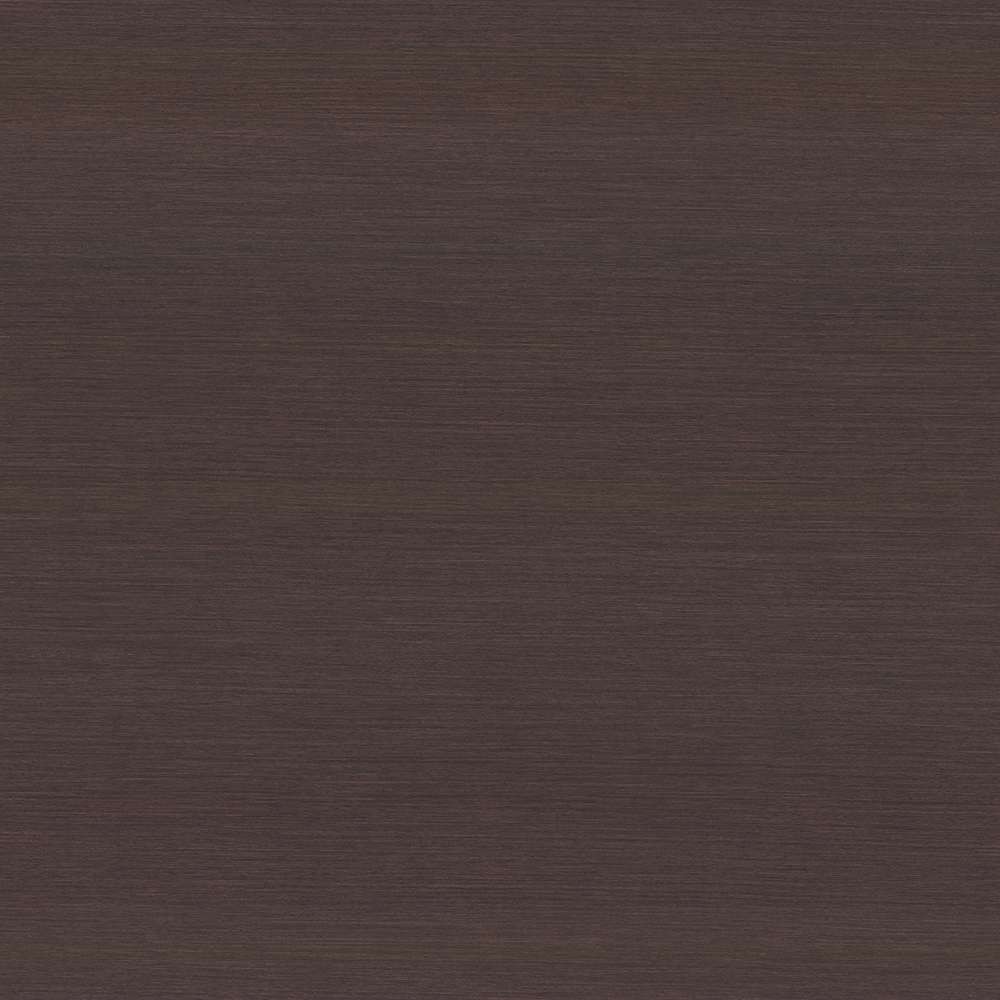
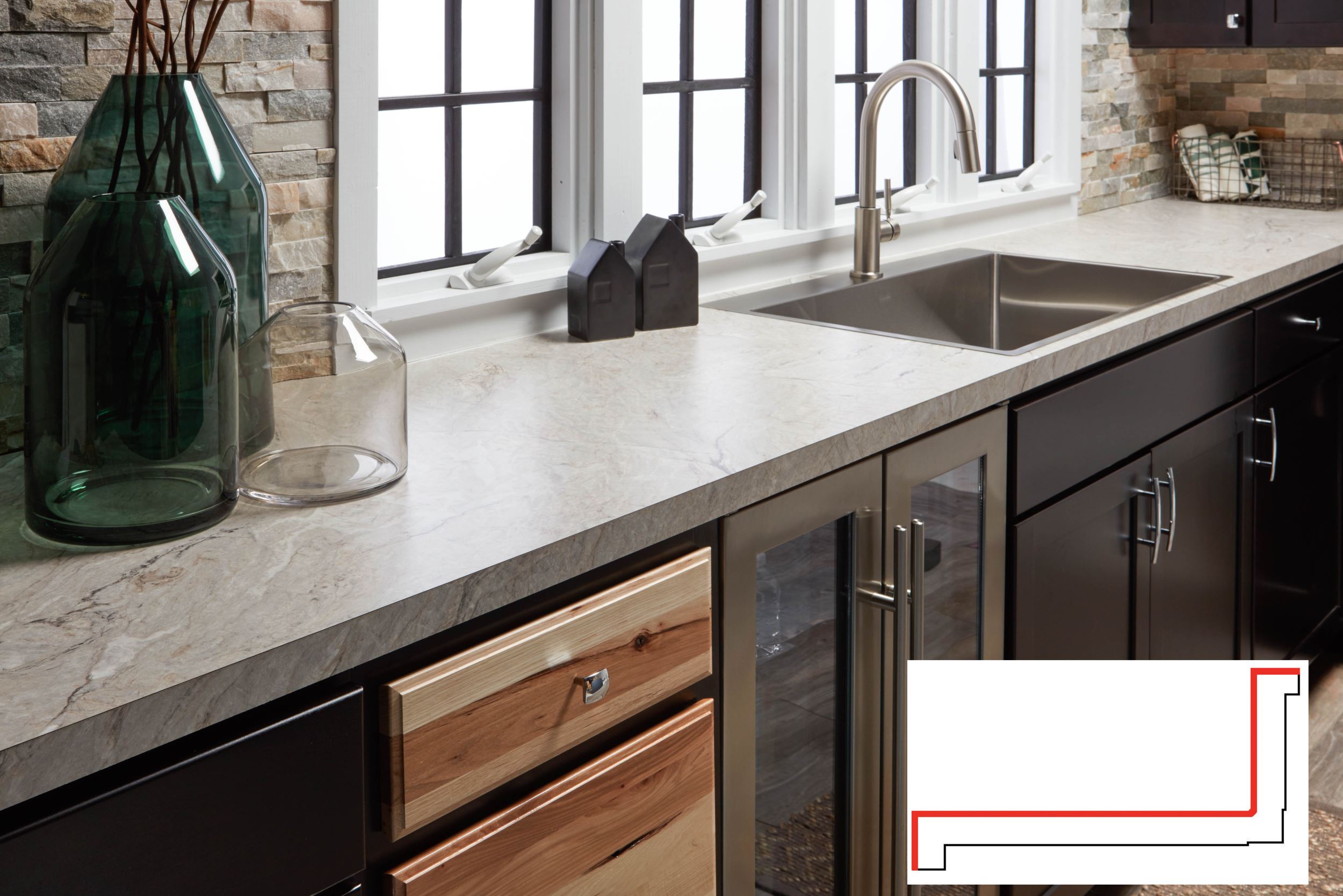
Special sizes for overall length, brush part, globules, filament, and special minimum and maximum diameters are designed and manufactured in Los Angeles, CA.Miller explains that the U.S. The Flex-Hone removes oxides and corrosion in order to produce a clean surface for the eddy current to test.Ĭustom Flex-Hones can be manufactured according to exact specifications. Any time there is removal or replacement of an aircraft fastener, inspection of the hole for cracking and stress propagation is required before reinstalling the fastener. BRM has many years of experience customizing the Flex-Hone tool, specifically for these types of demanding applications.Īccording to Mike Miller, BRM's vice president of global sales, "Currently, one of the biggest applications where the Flex-Hone tool is used is in the surface preparation for eddy current testing. That is where Brush Research Manufacturing (BRM) enters the picture. Beyond knowing the practice, knowing the companies that actively provide the tools for this is necessary as well. Any aerospace company working in this field needs to know the best practices for chamfered honing to industry standards. The requirement for blending chamfered holes is growing rapidly in the jet engine industry.
